This was a absolutely massive project. Two 36’ walnut waterfall tables, one 30’ table and one 22’ table for a grand total of 124 feet of 6 foot-wide solid walnut. That’s more than 40% of the length of a football field. In most pictures below, you only see one of the tables at a time because of their size.
The tables are completely bespoke, designed for a large marketing firm to use as work tables for graphic designers and programmers, with integrated power and cable storage for anything they could possibly throw at them. The tables have no obstructions along the sides, so users can sit wherever they like along the table with no legs to block chairs or file carts.
Each table has a continuous cable channel running the entire length of the table, with solid walnut doors that flip-up for access to concealed power strips and cable storage. When the doors are flipped down, soft-close hinges protect users’ fingers and a one inch gap provides room for cables to pass up-and-out to computers and other devices.
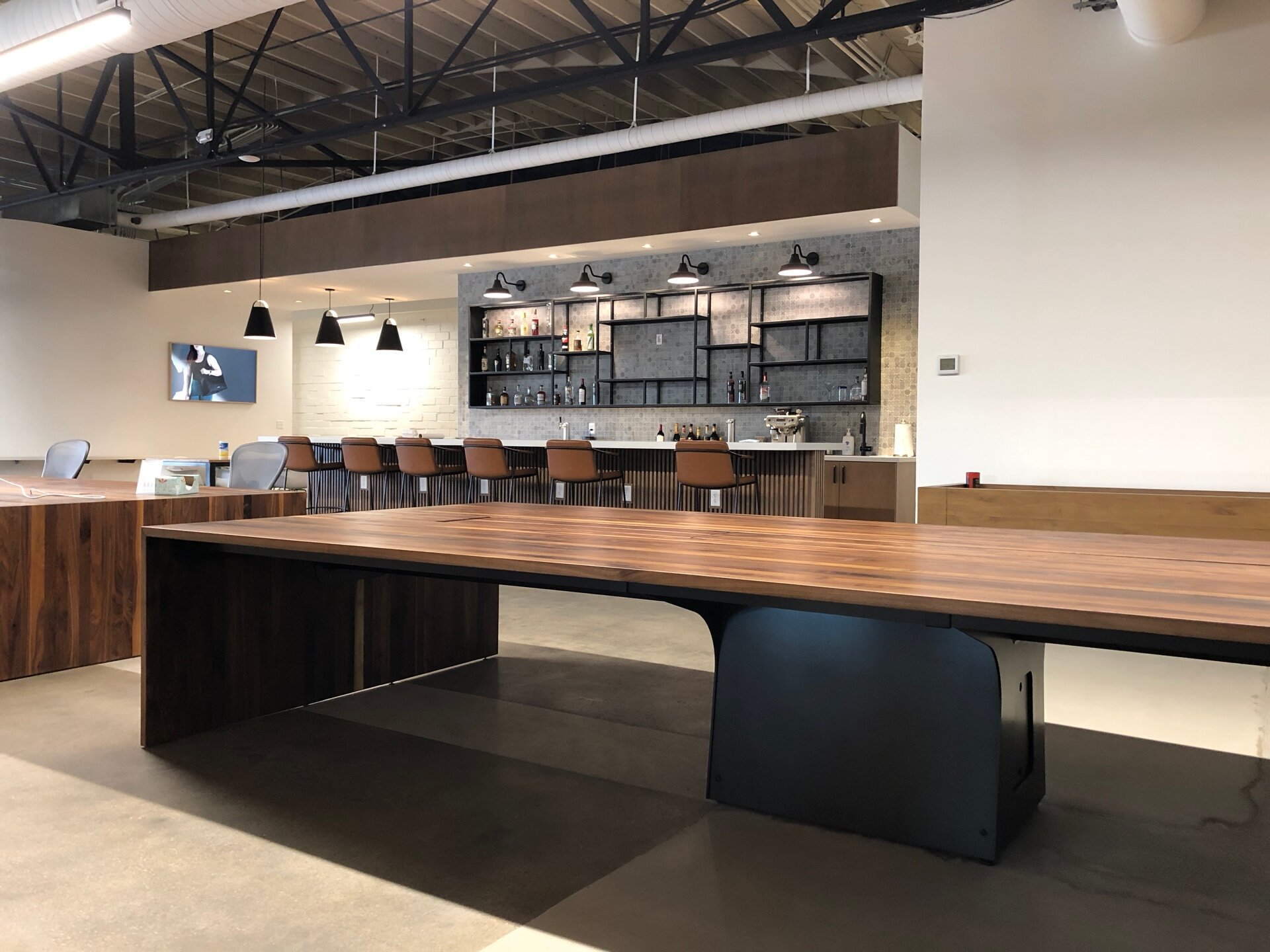
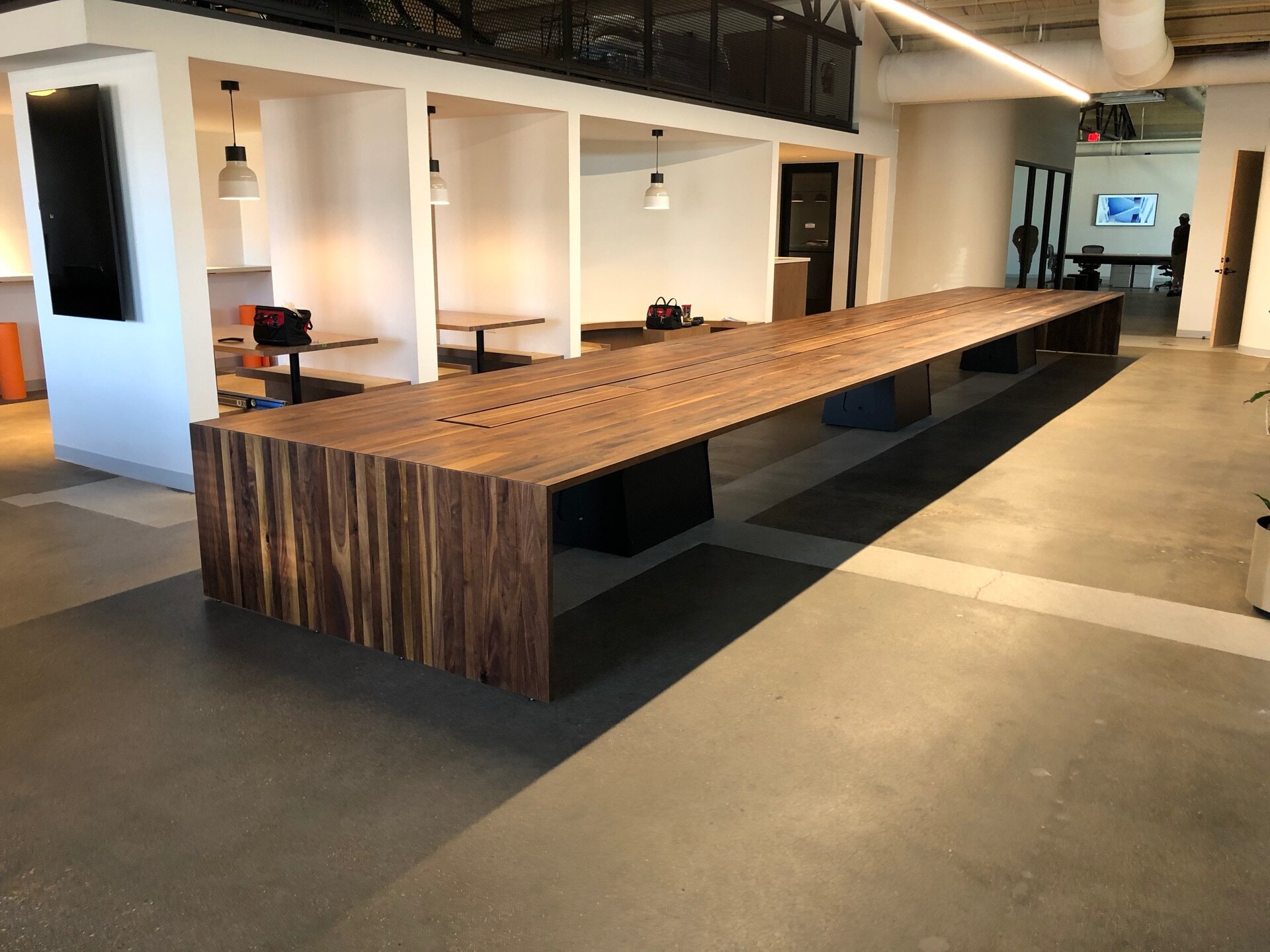
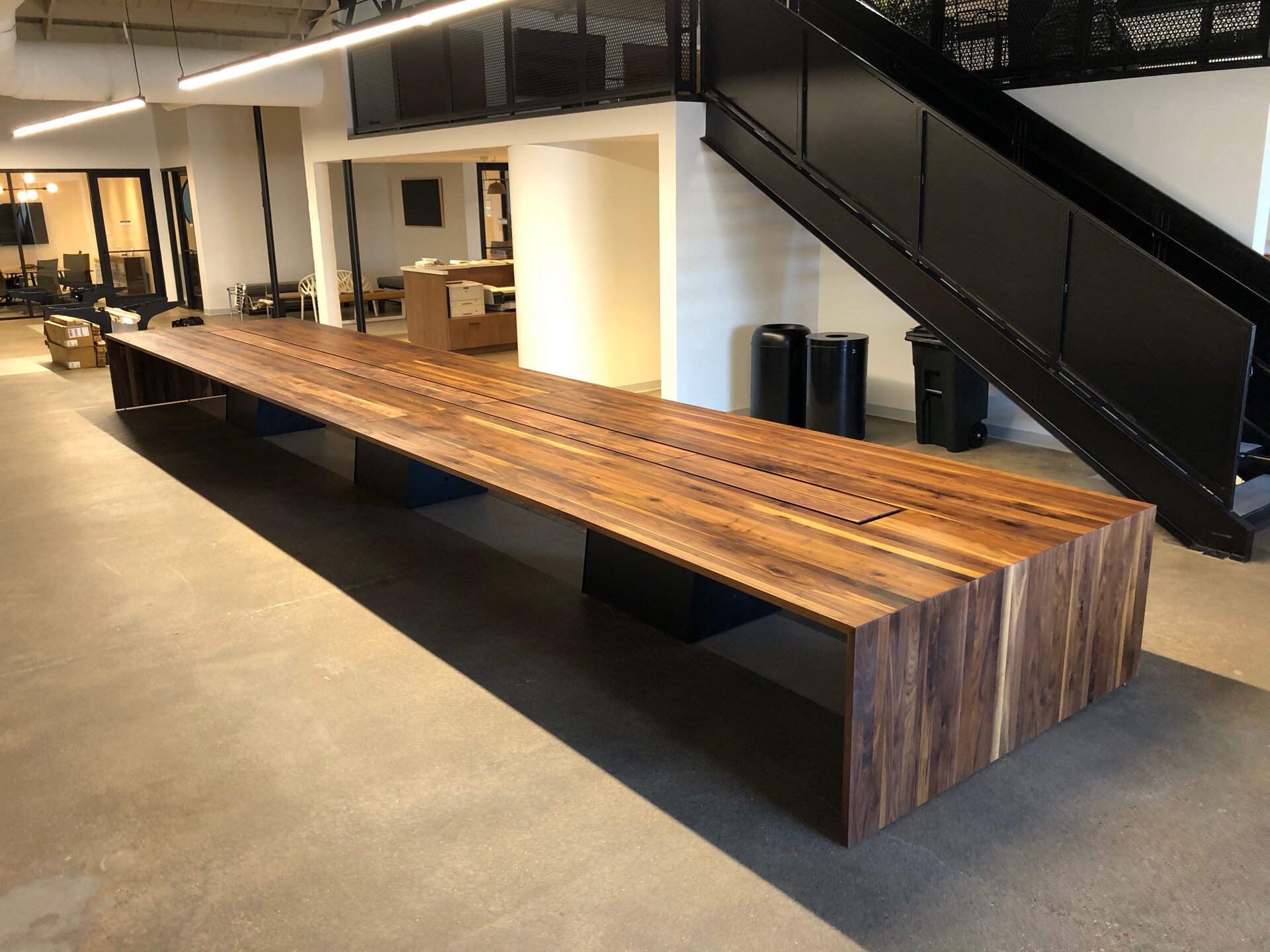
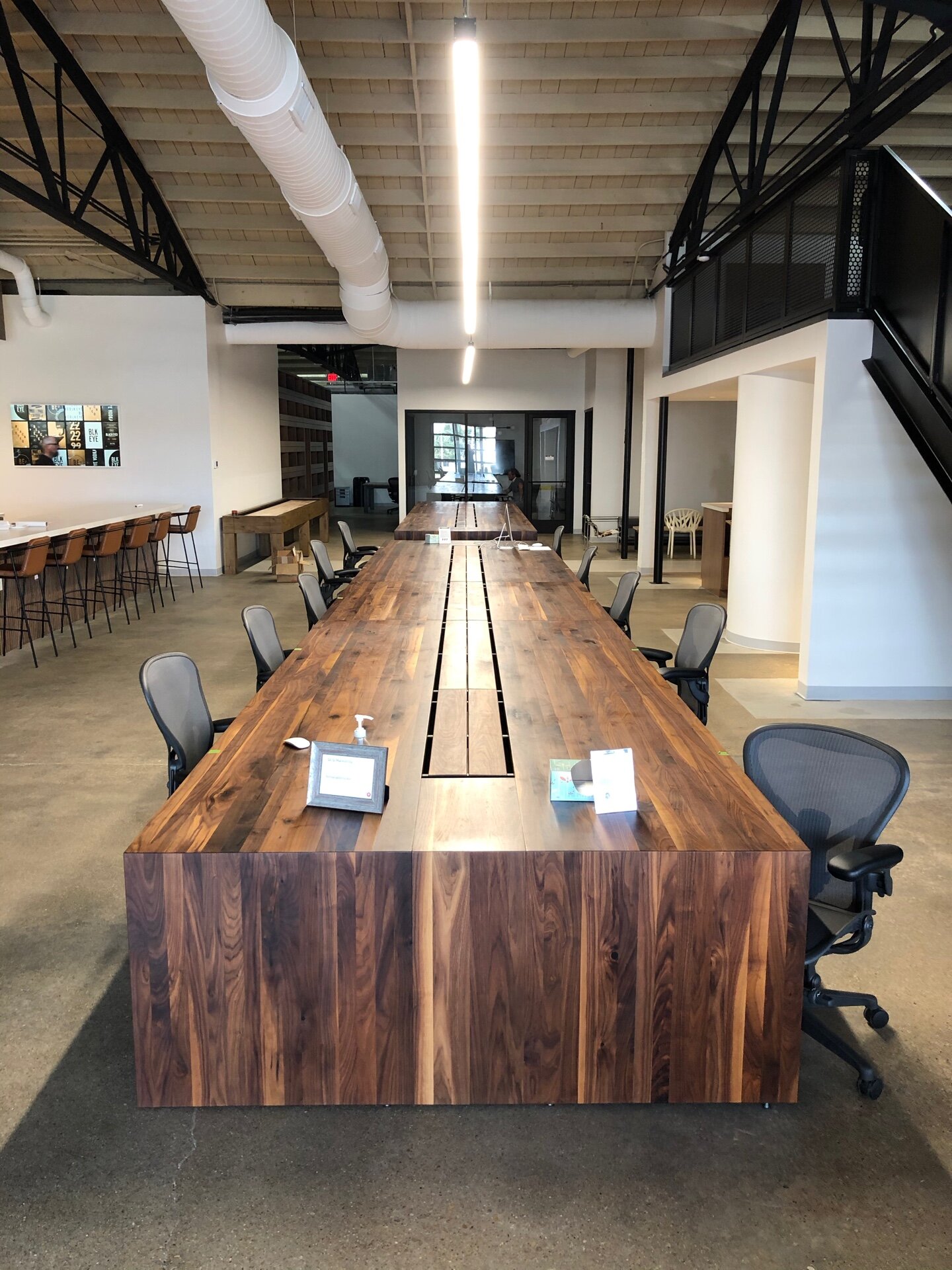
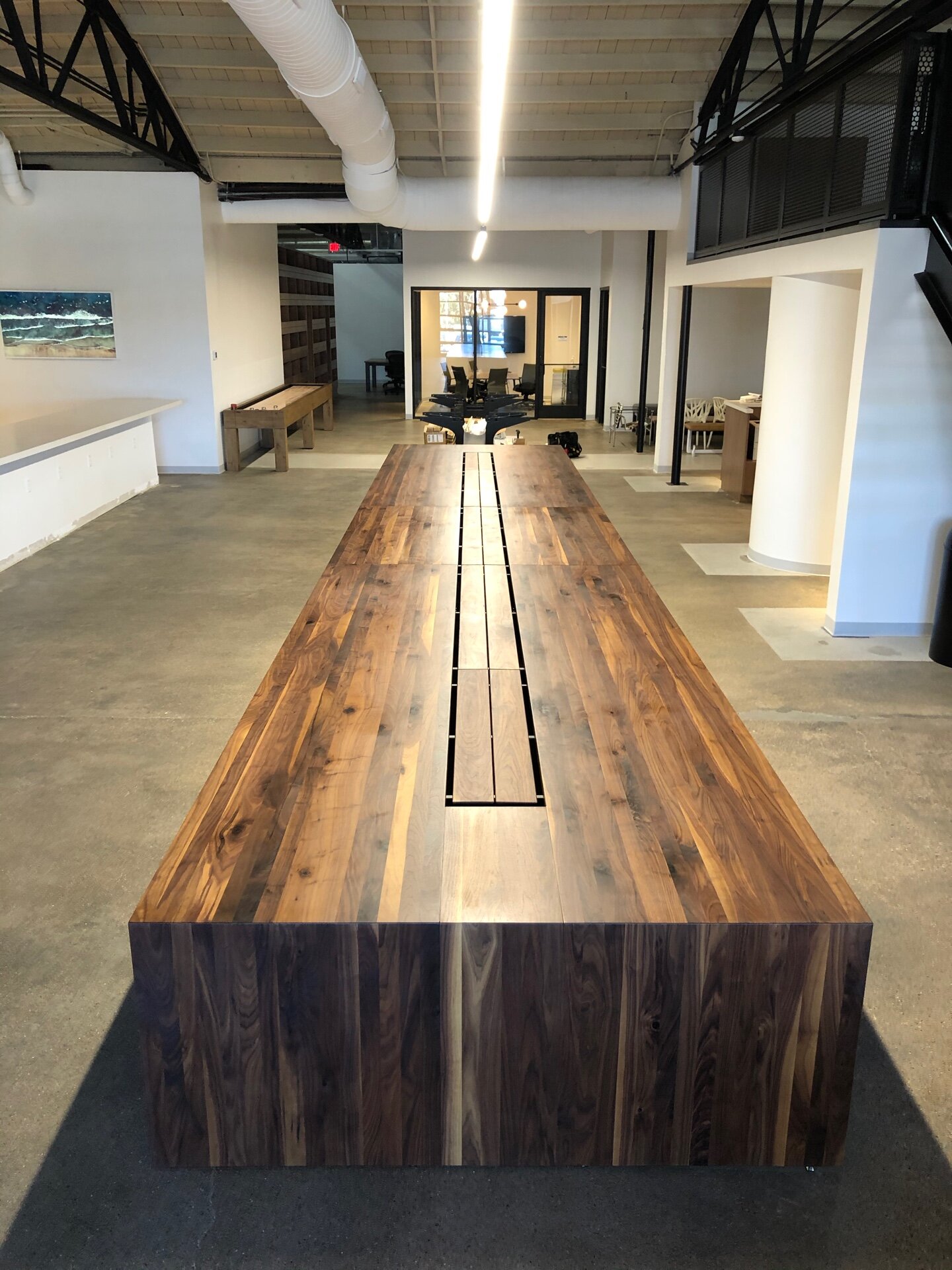
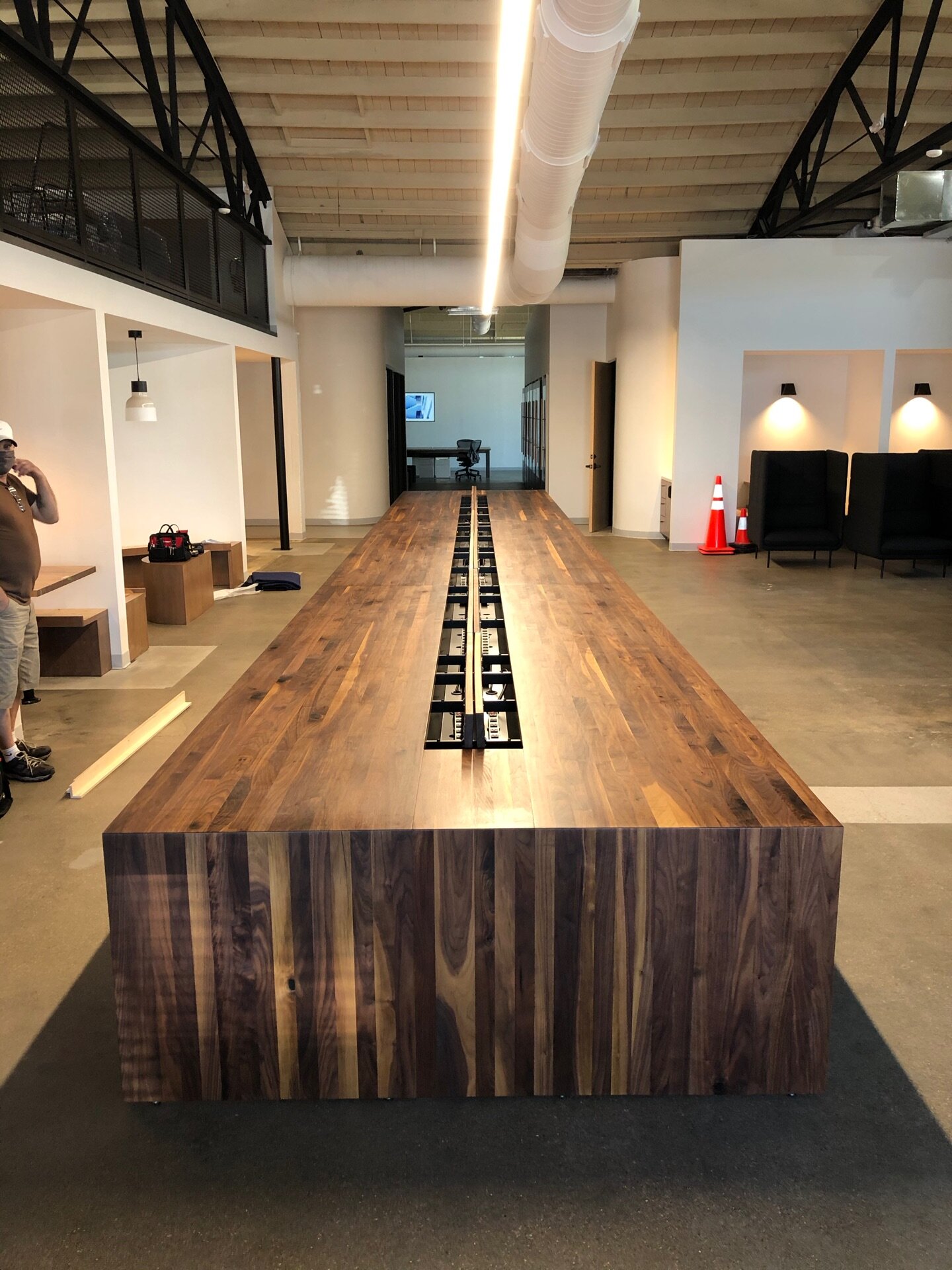
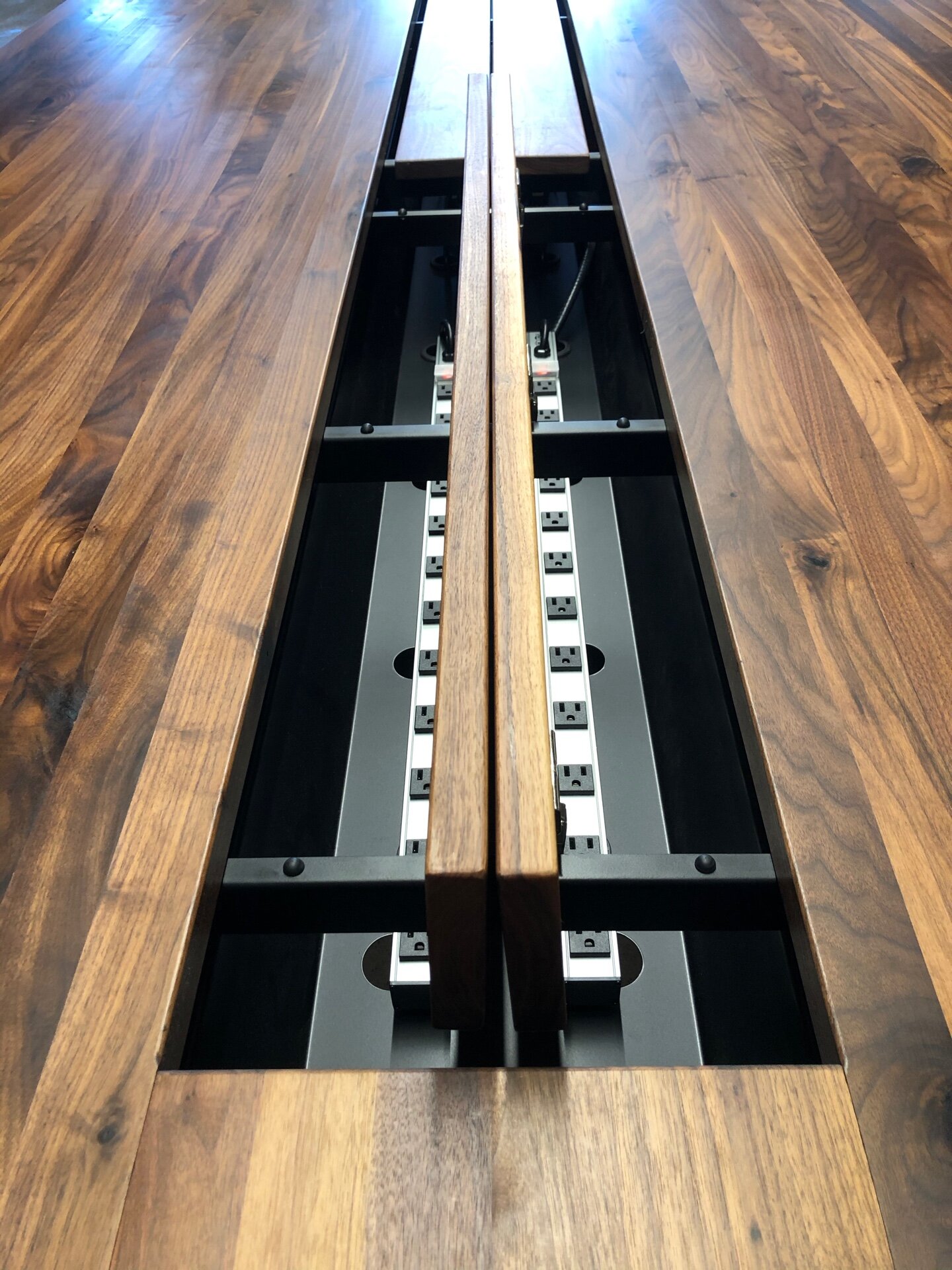
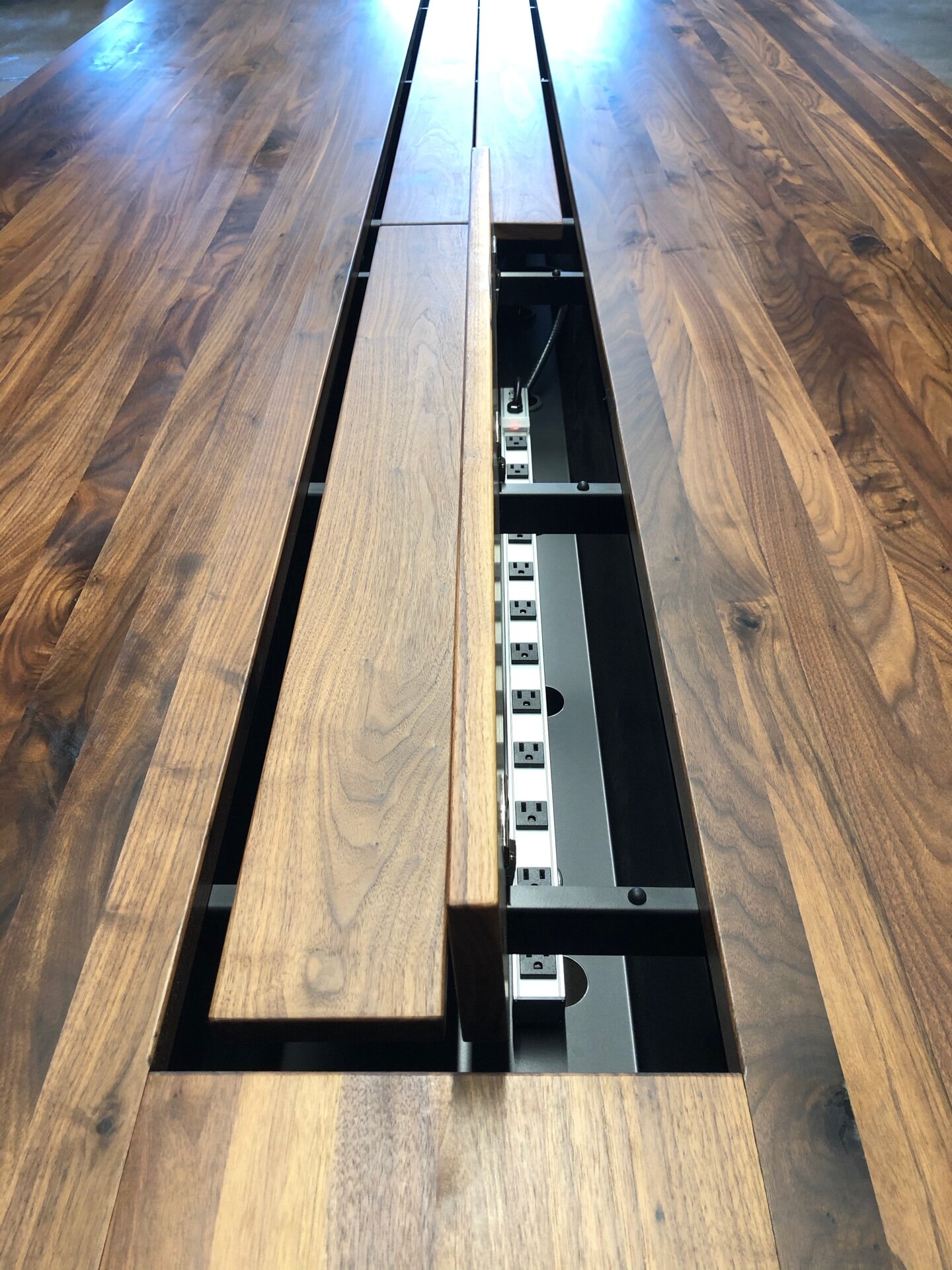
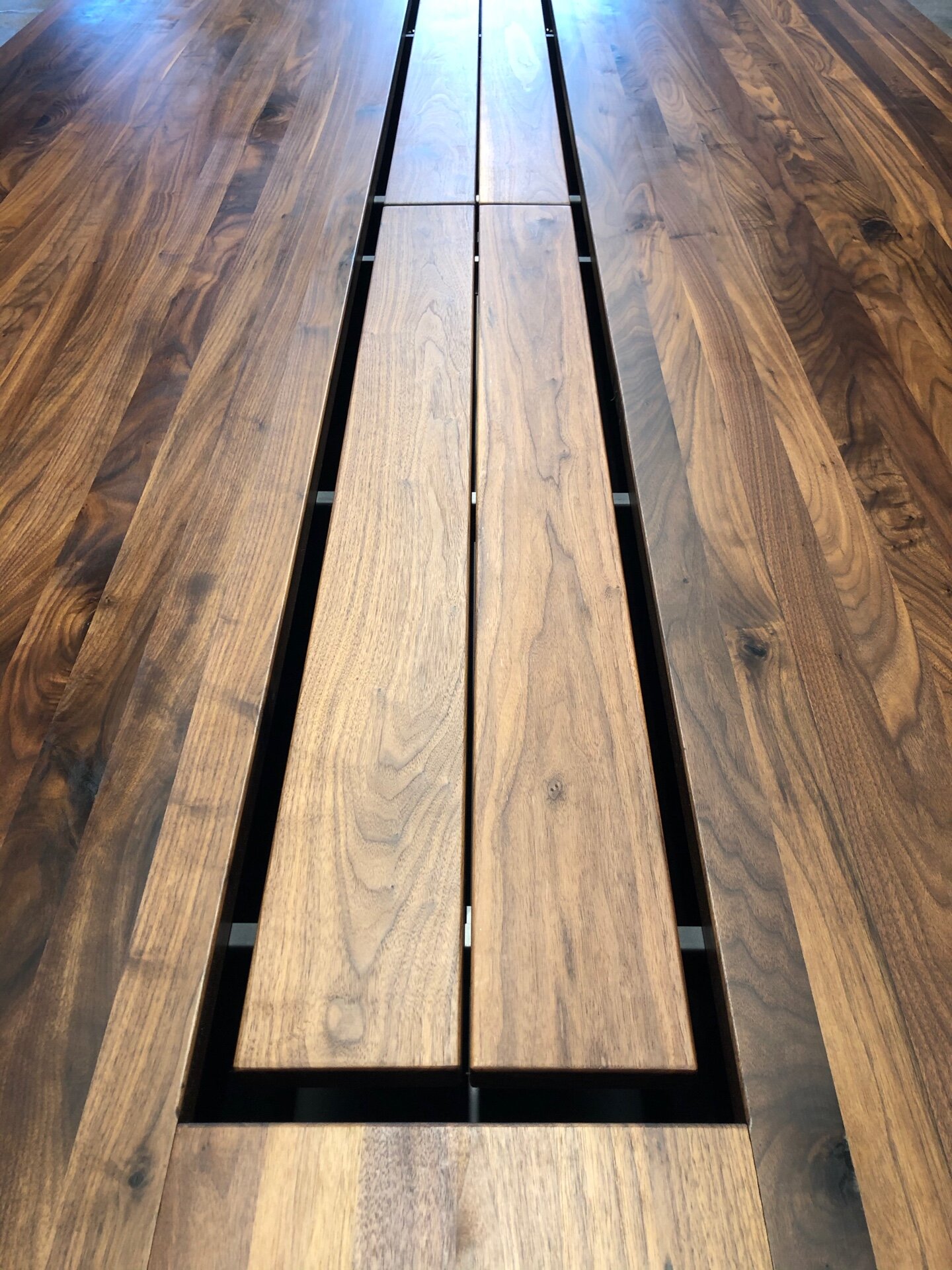
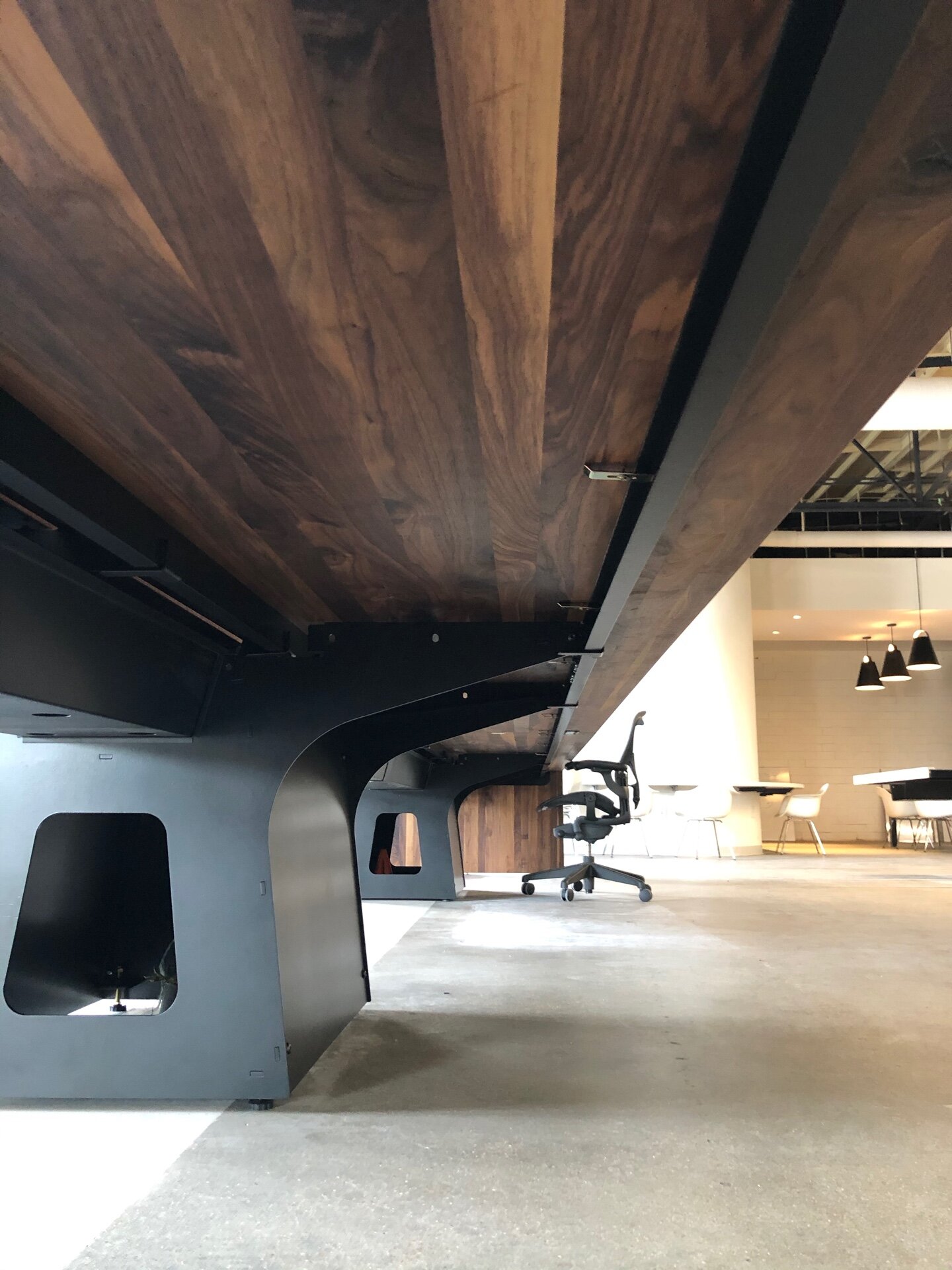
The table tops were fabricated in 12’ sections with full length 2” staves. The raw walnut boards were cut, glued up and planed by a local supplier to produce more than two dozen 13’-14’ raw tops, then all knots and imperfections were repaired and filled with tinted epoxy to maintain the character of the natural walnut. The epoxy work and subsequent joinery and finishing were completed entirely in-house. The waterfall ends were so large and numerous that we designed and fabricated custom clamps to help flatten and hold the joints while the glue cured to full strength. Once glued, cut to length and sanded, all surfaces were finished with Rubio Monocoat Pure, a hard oil finish that will provide a tough yet maintainable work surface for many years to come.
The table tops sit on custom steel frames, designed and engineered entirely in-house to accommodate the long table lengths and irregular concrete floors of a nearly 70 year old industrial building renovated for their new home. The bases consist of laser-cut steel that is welded to form assemblies that were easy to transport flat and then bolt together like a giant erector set on-site. The cable channels are turret-punched and press-formed sheet steel, and the long structural rails are bar channel that attaches to the bases with a common bracket that is also used throughout the tables to hold the crossmembers for the flip-up doors. And all the steel was powder coated for a tough lasting finish. The long rails provide continuous support along the entire length of the tables, and the tops are attached in a way that allows them to “breathe” as the wood changes dimension over time with temperature and humidity changes.
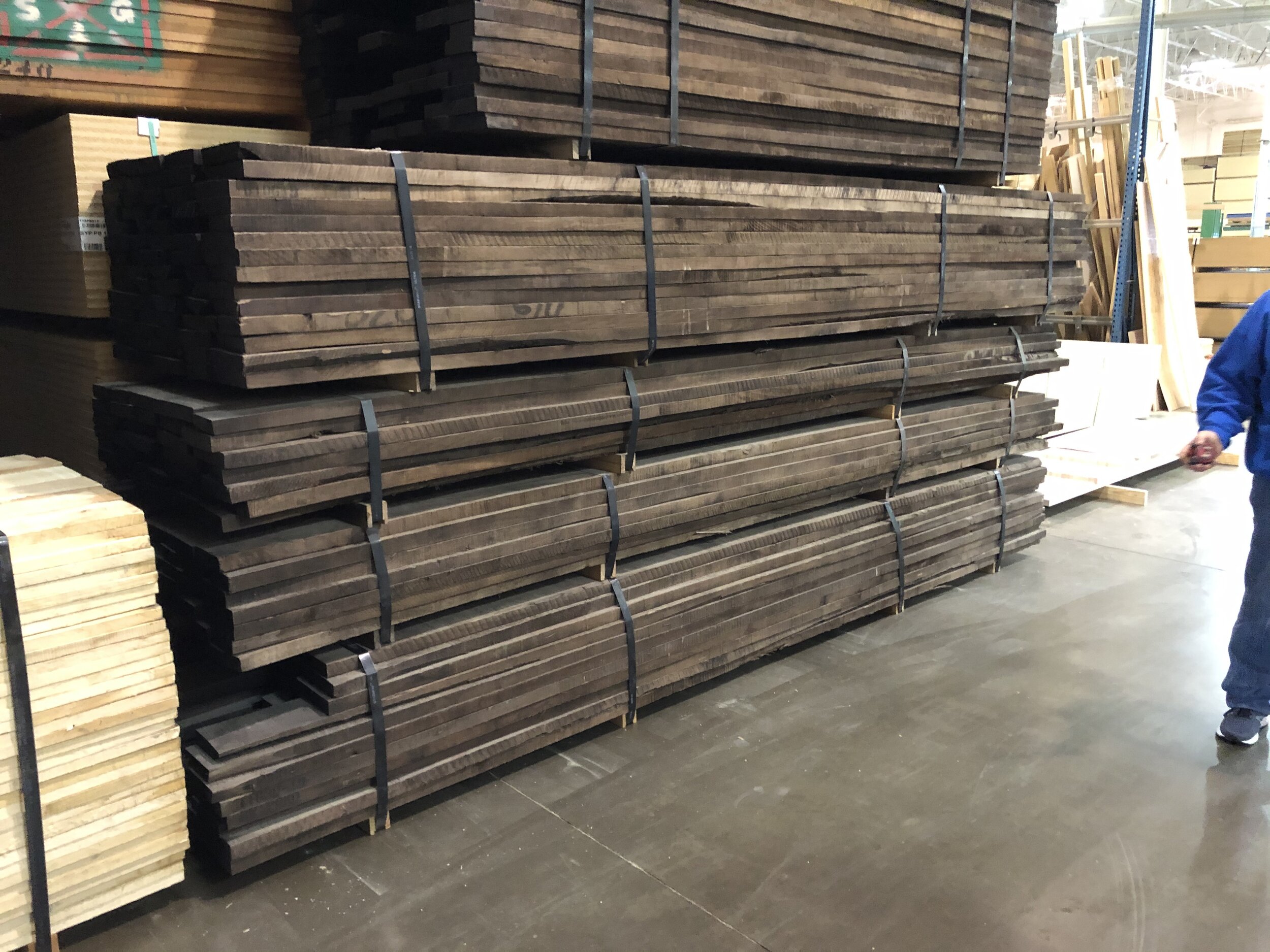
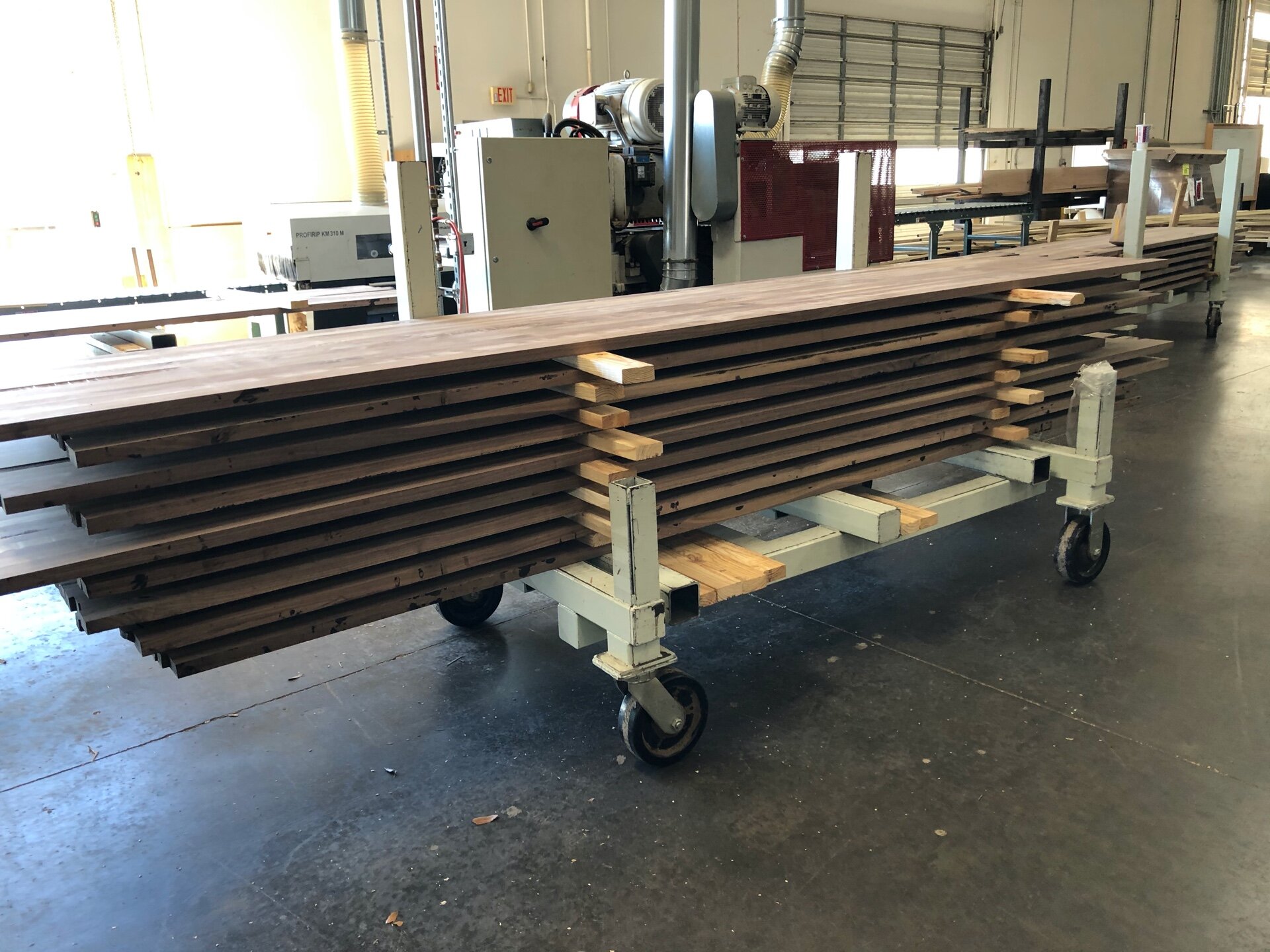
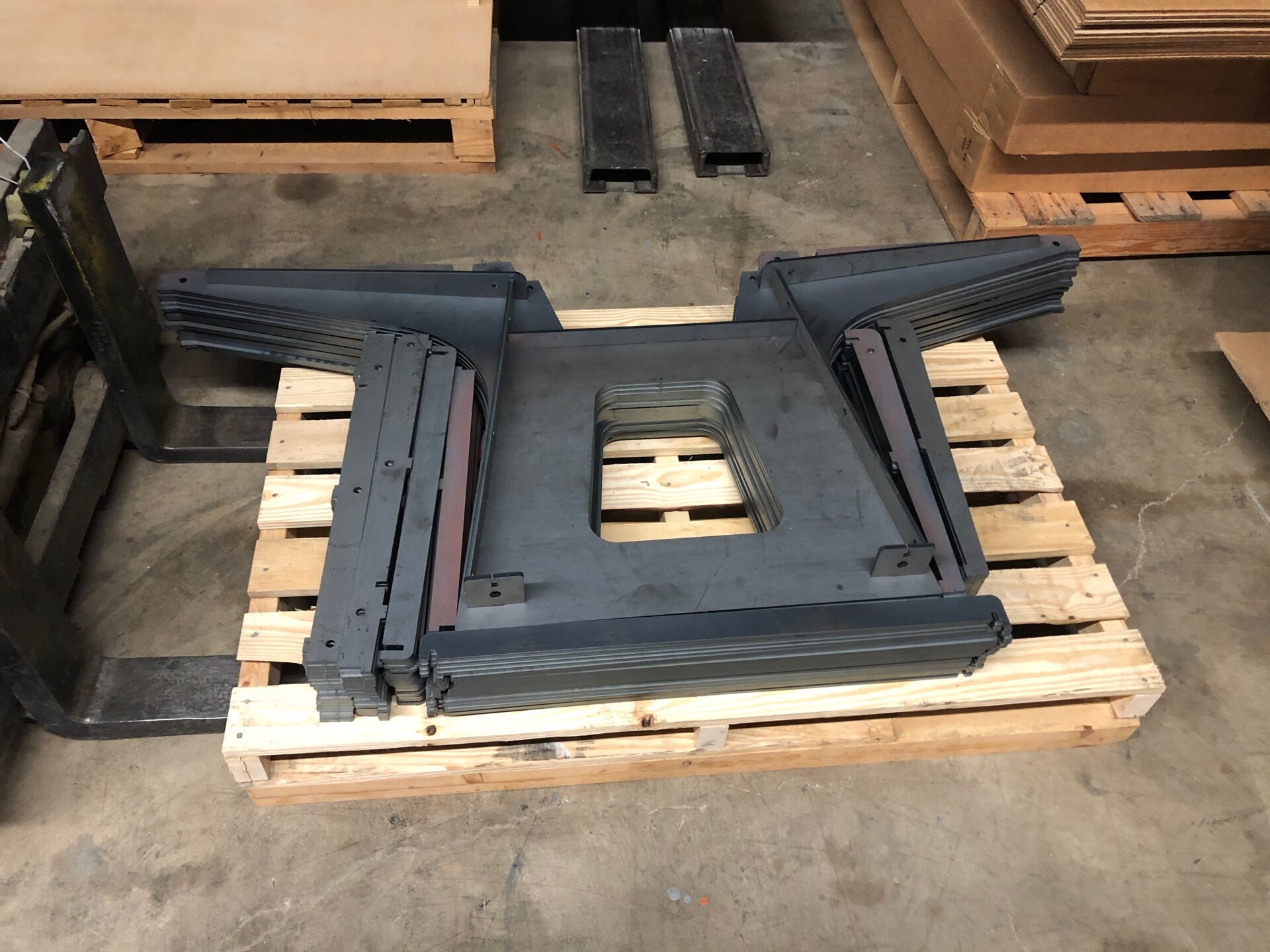
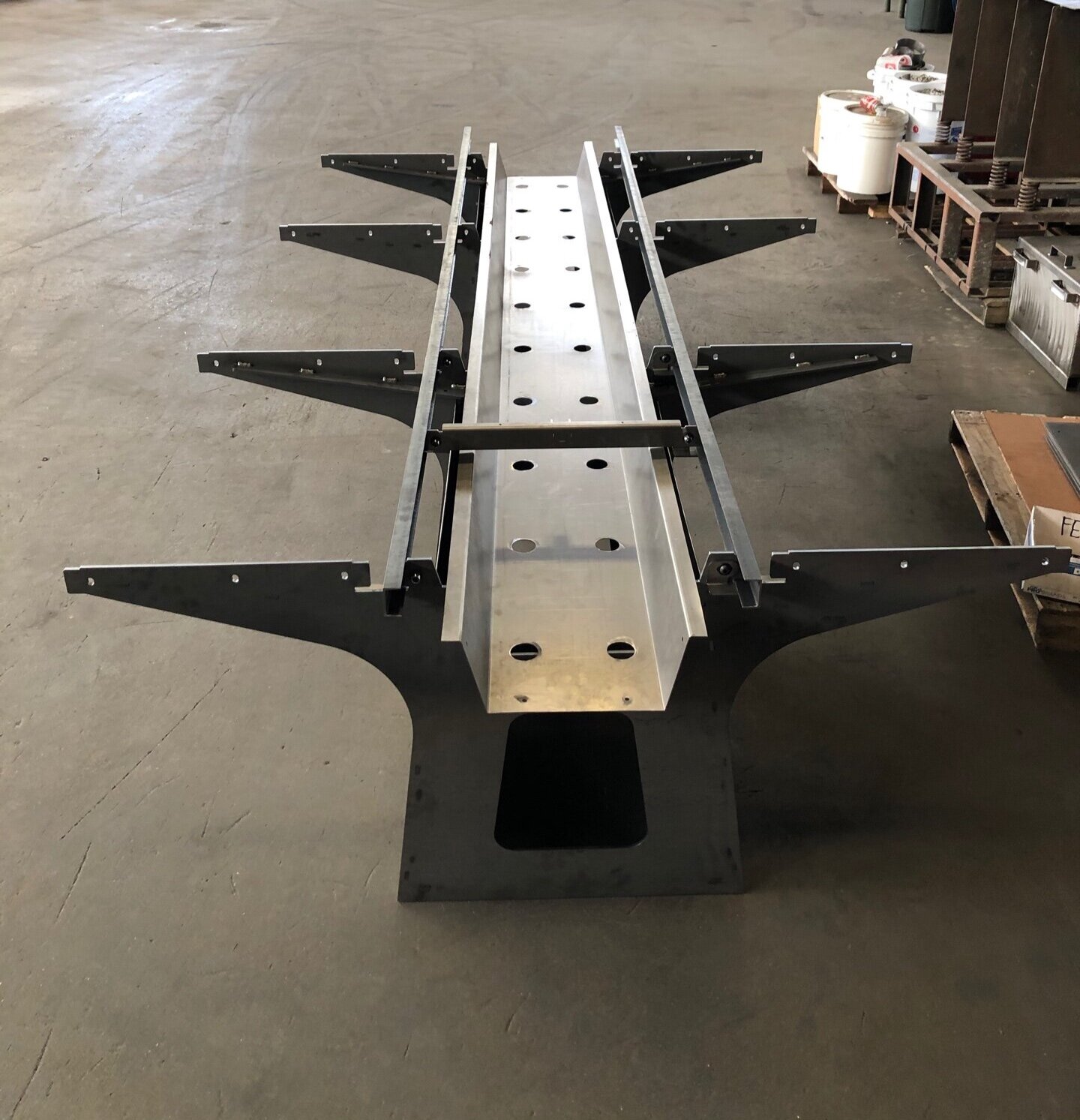
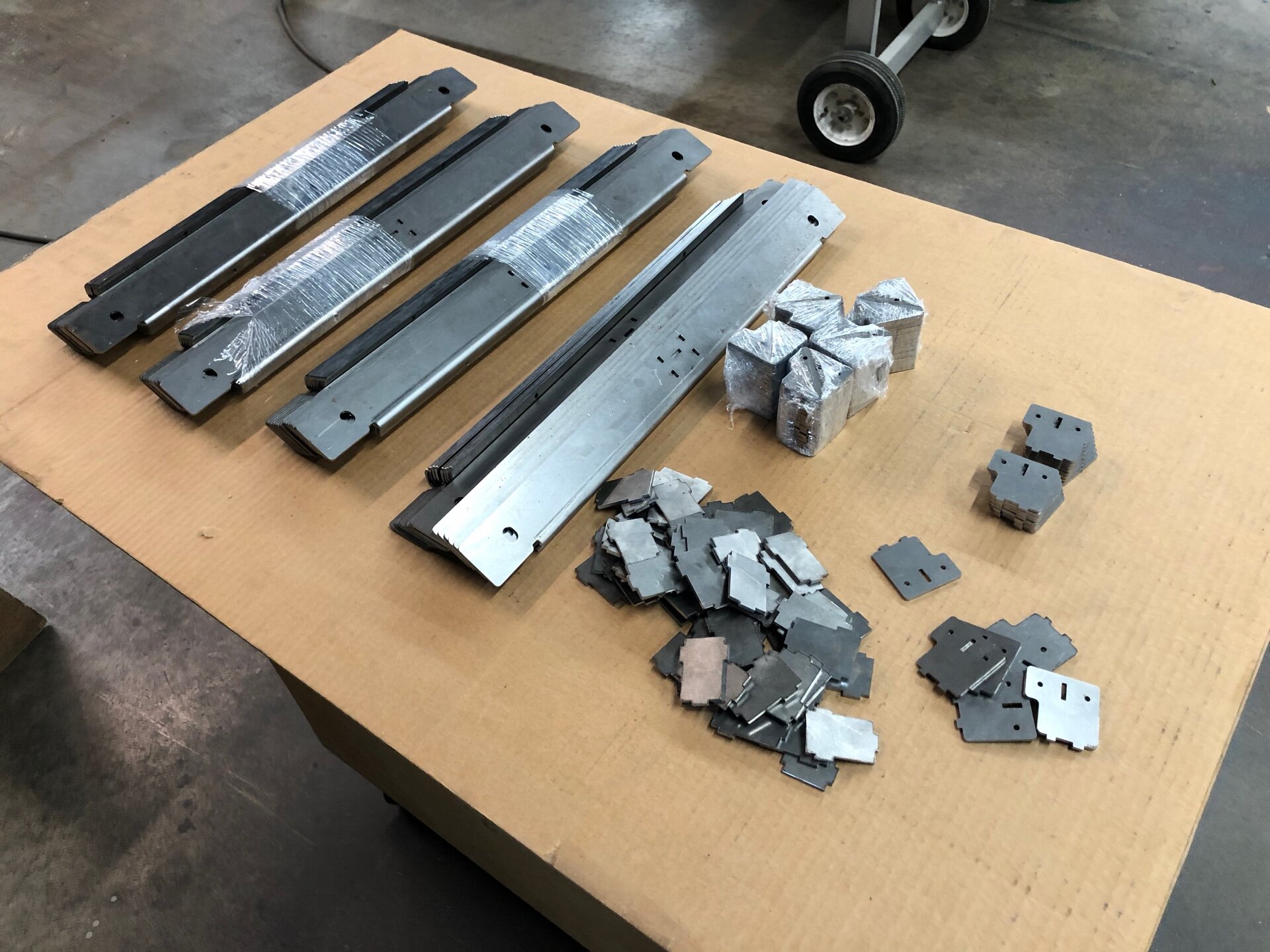
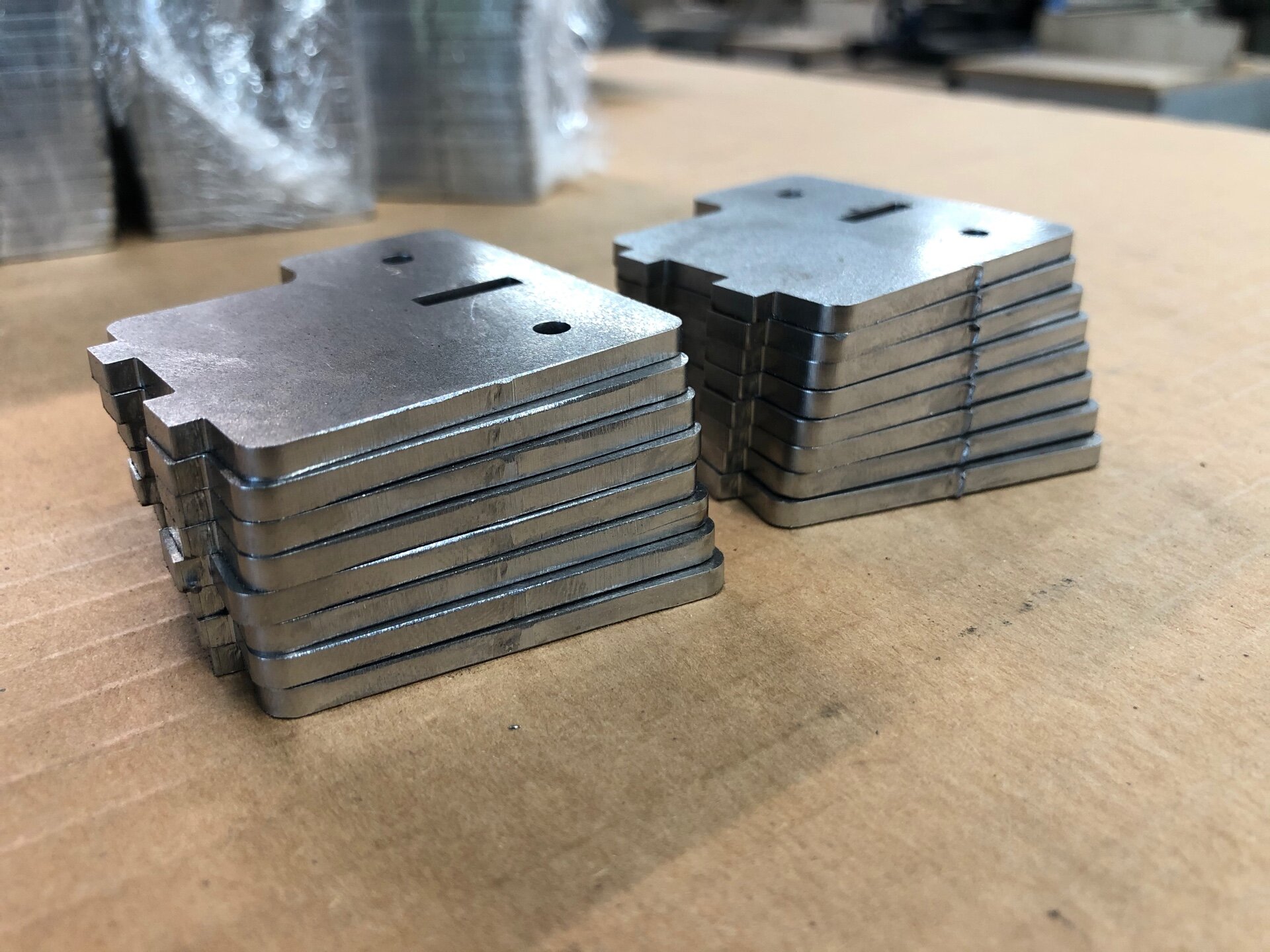
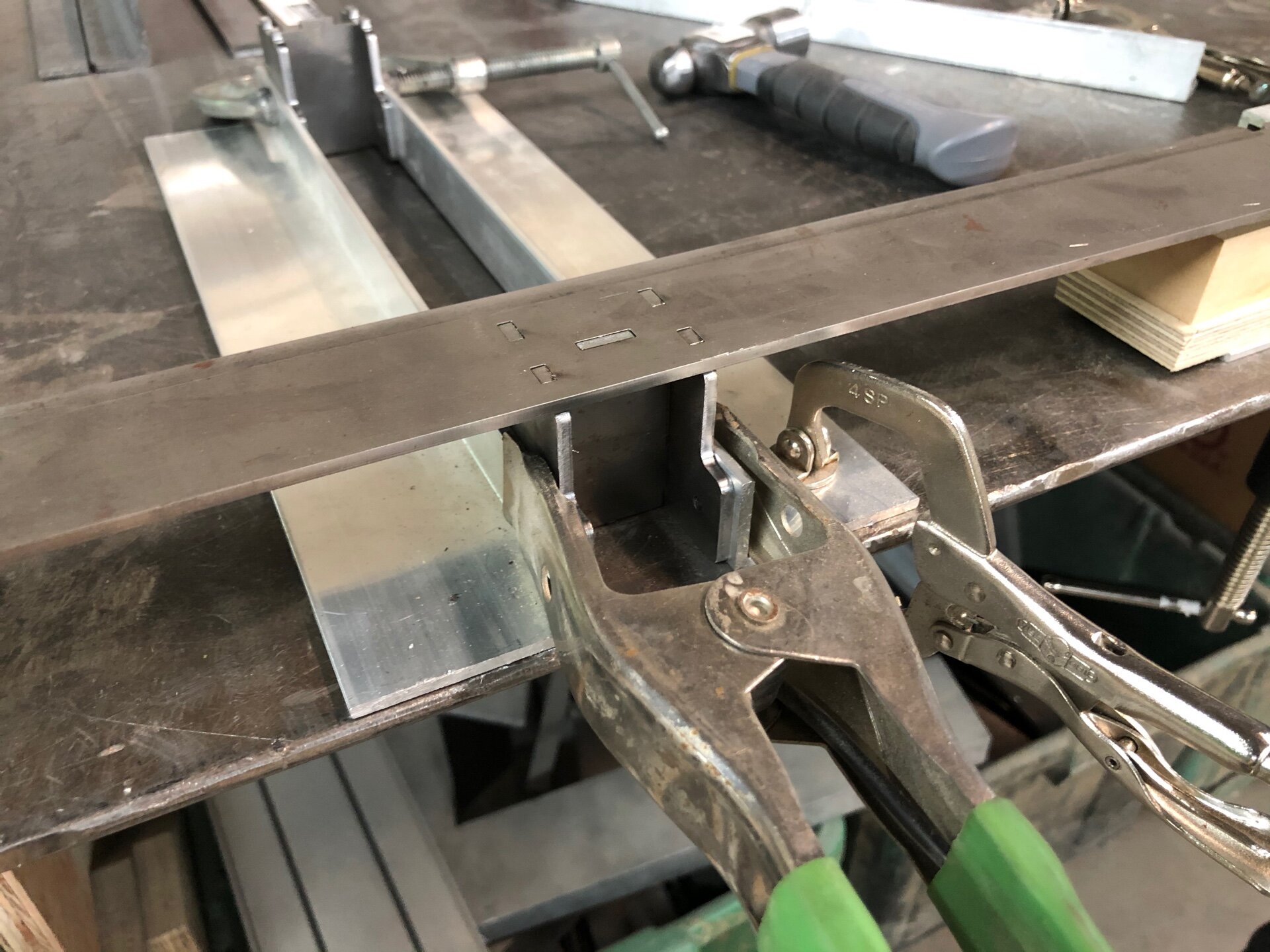
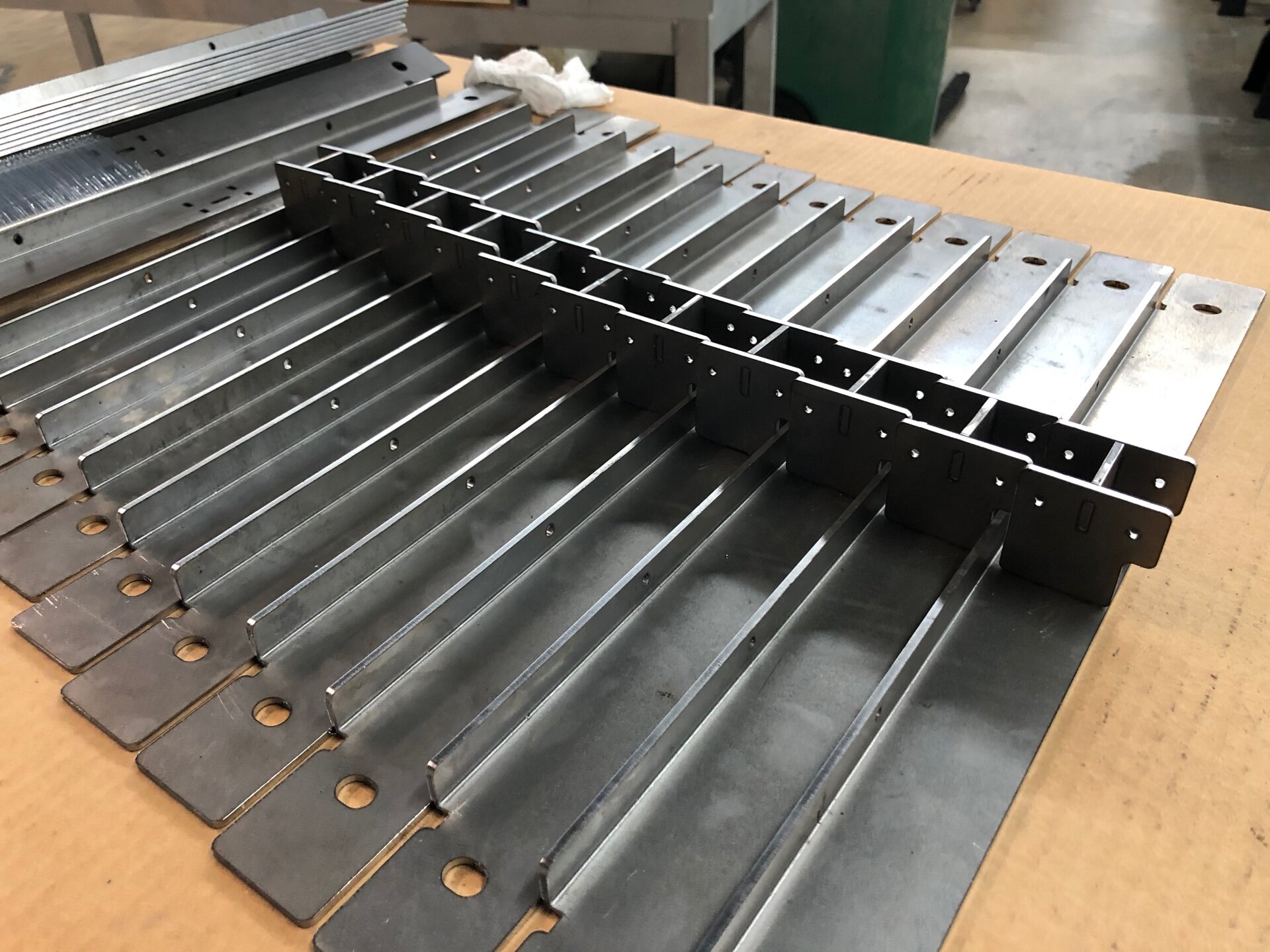
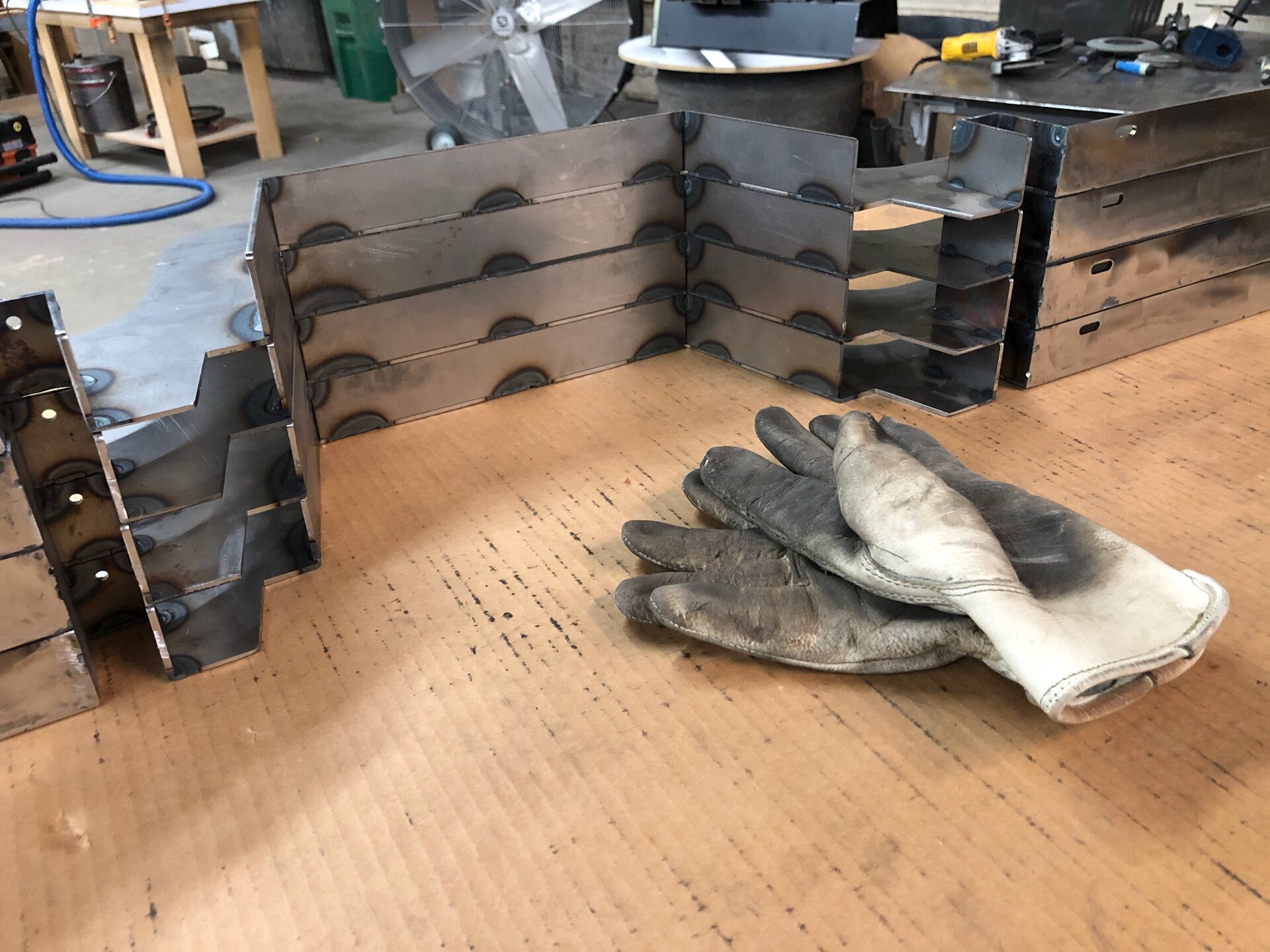

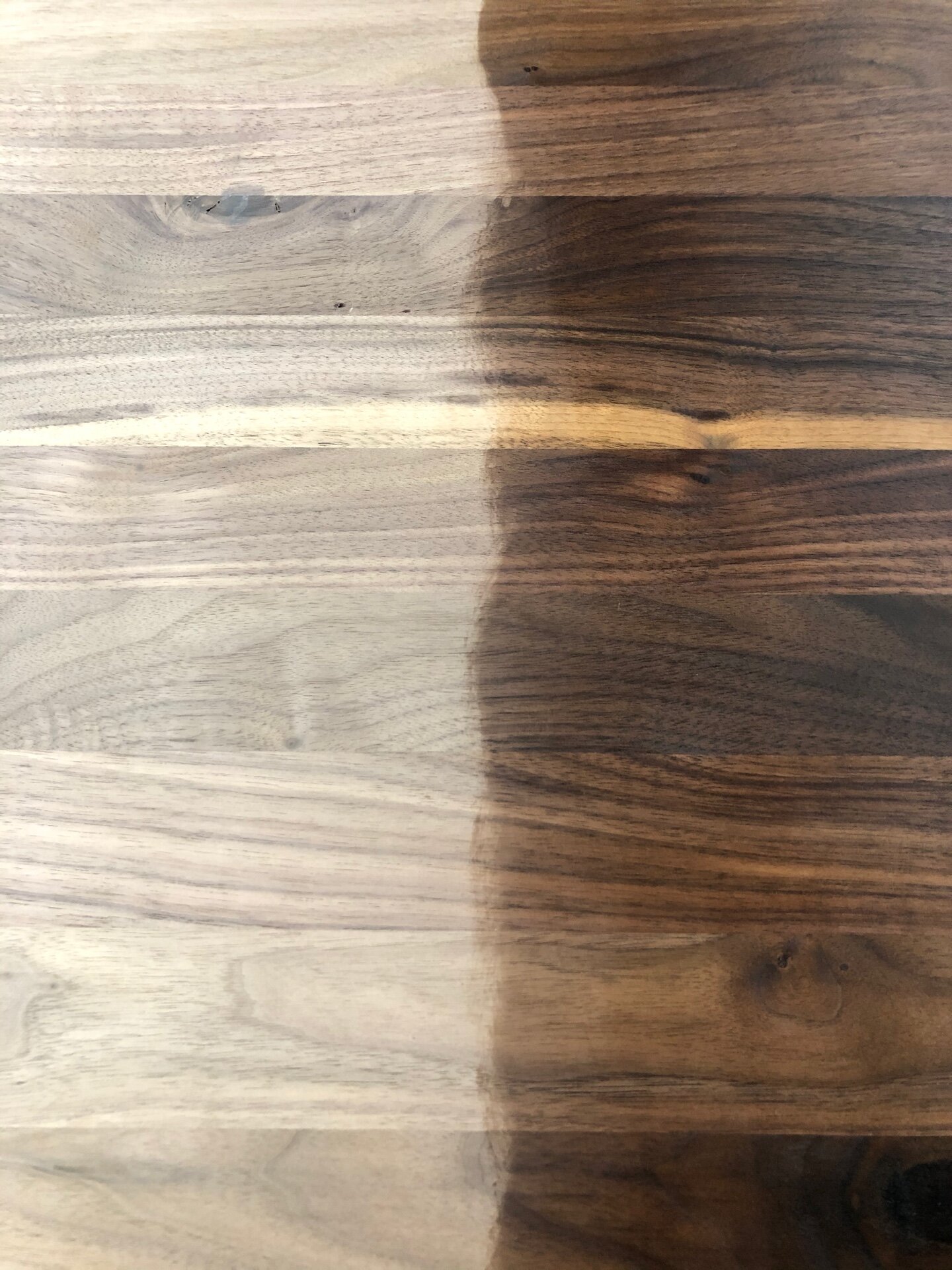
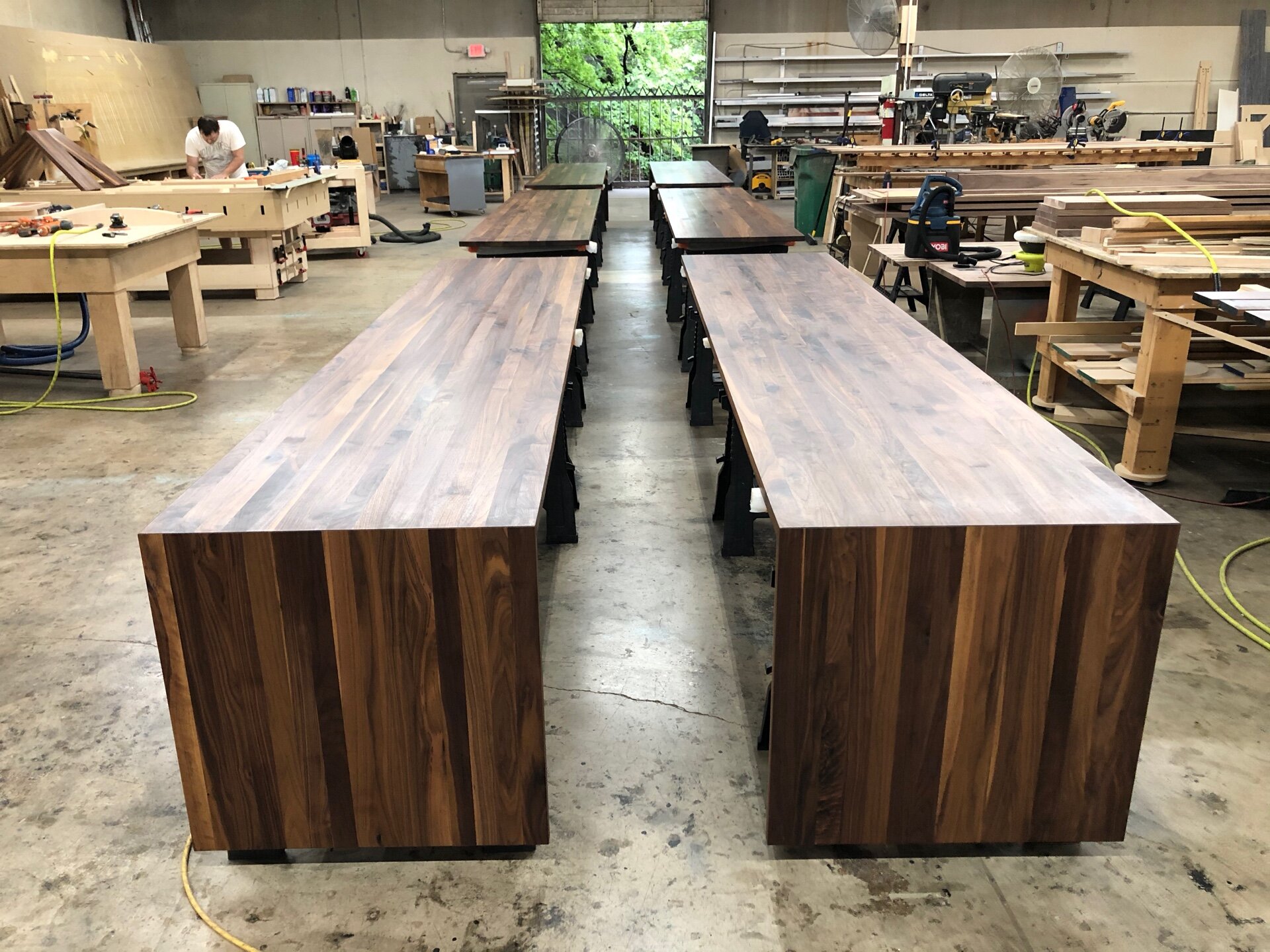
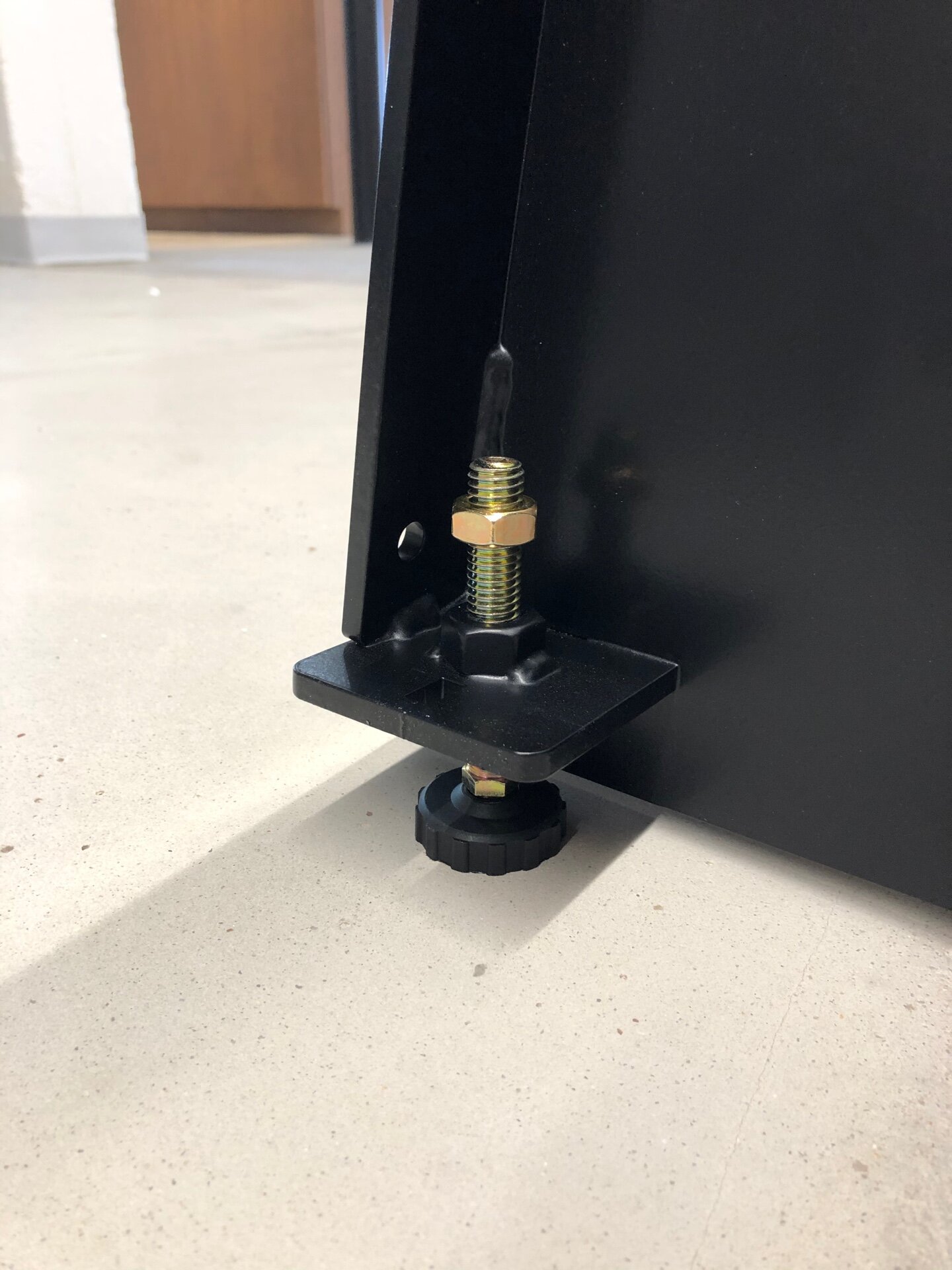
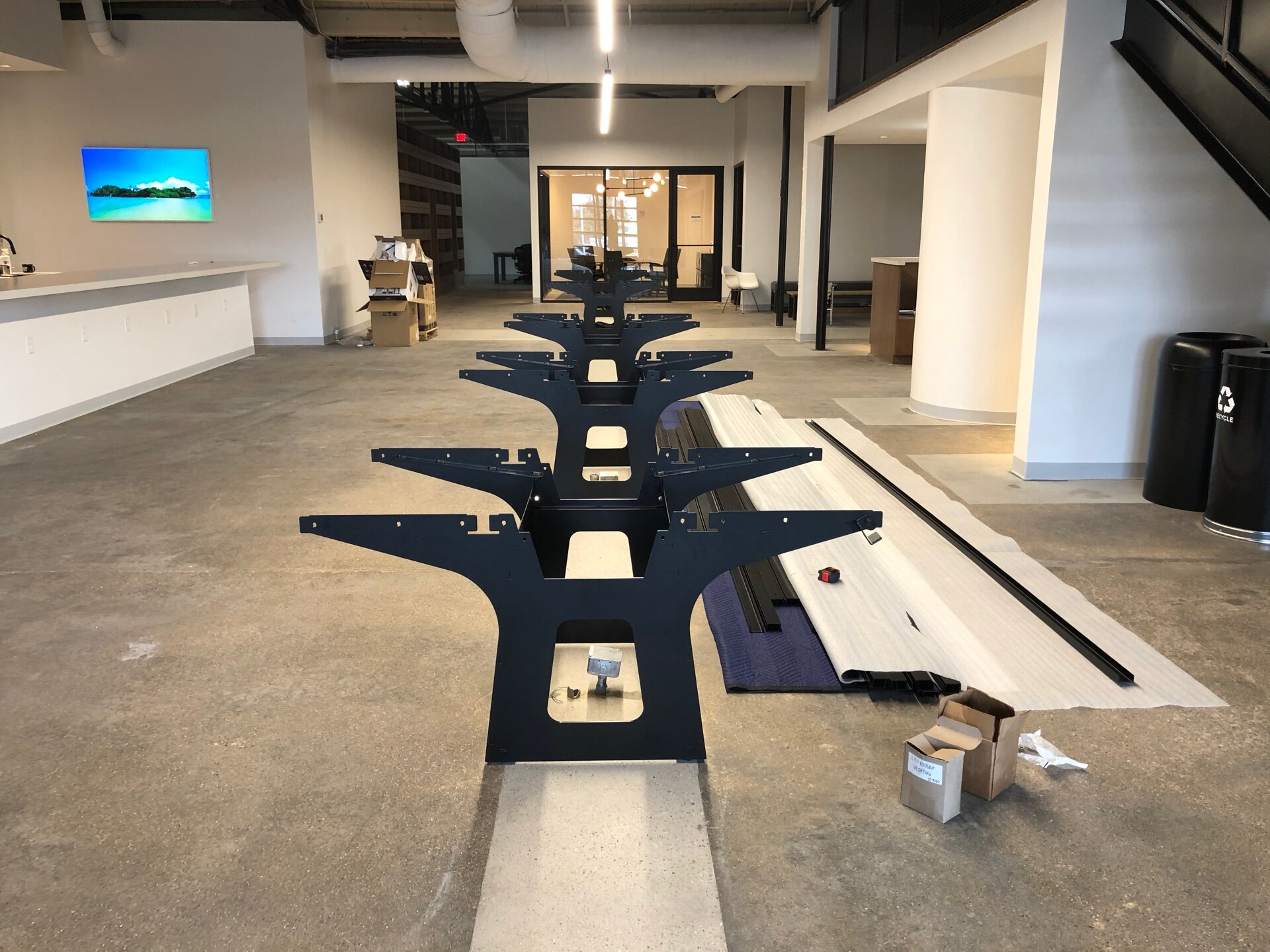
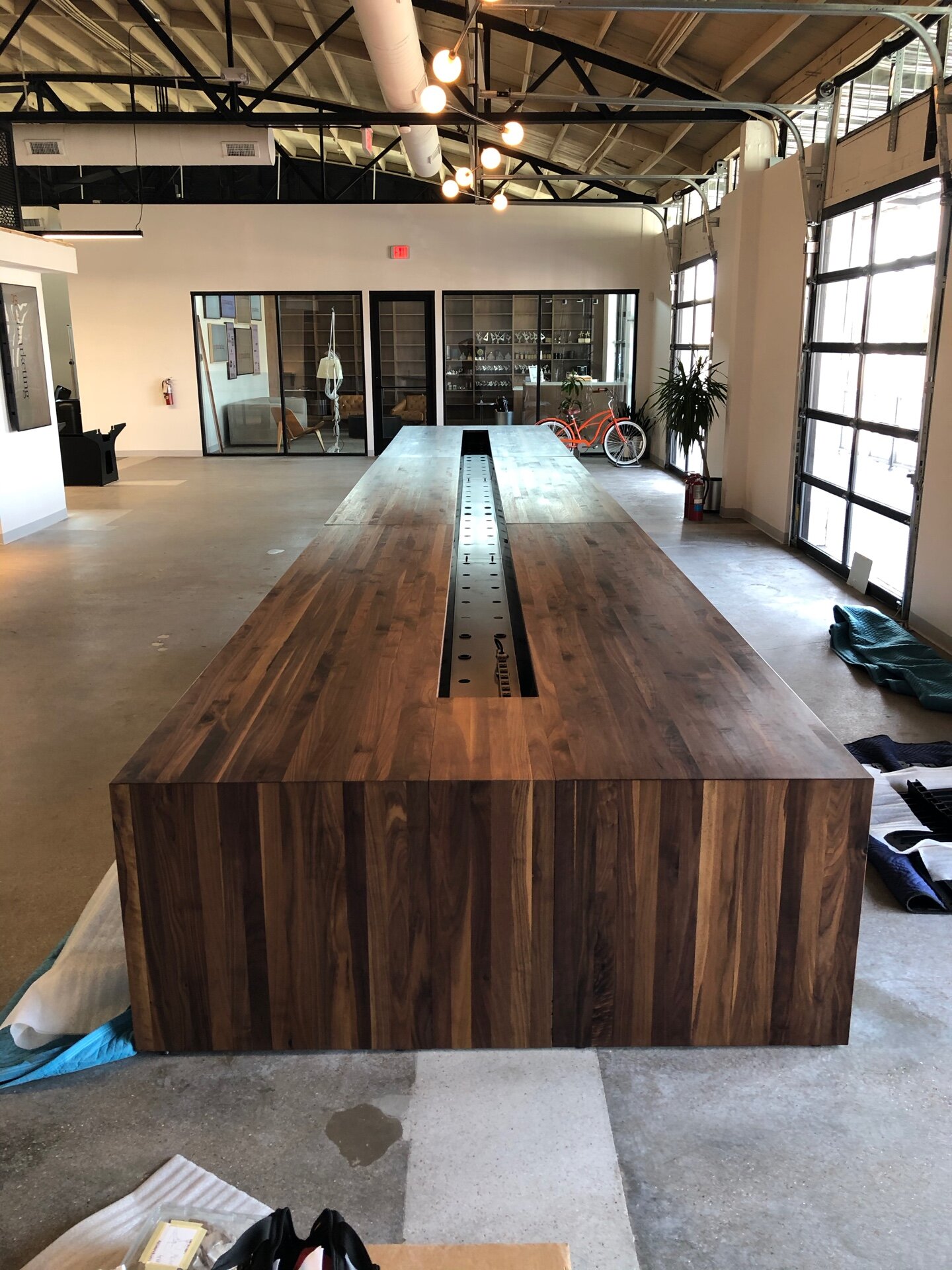
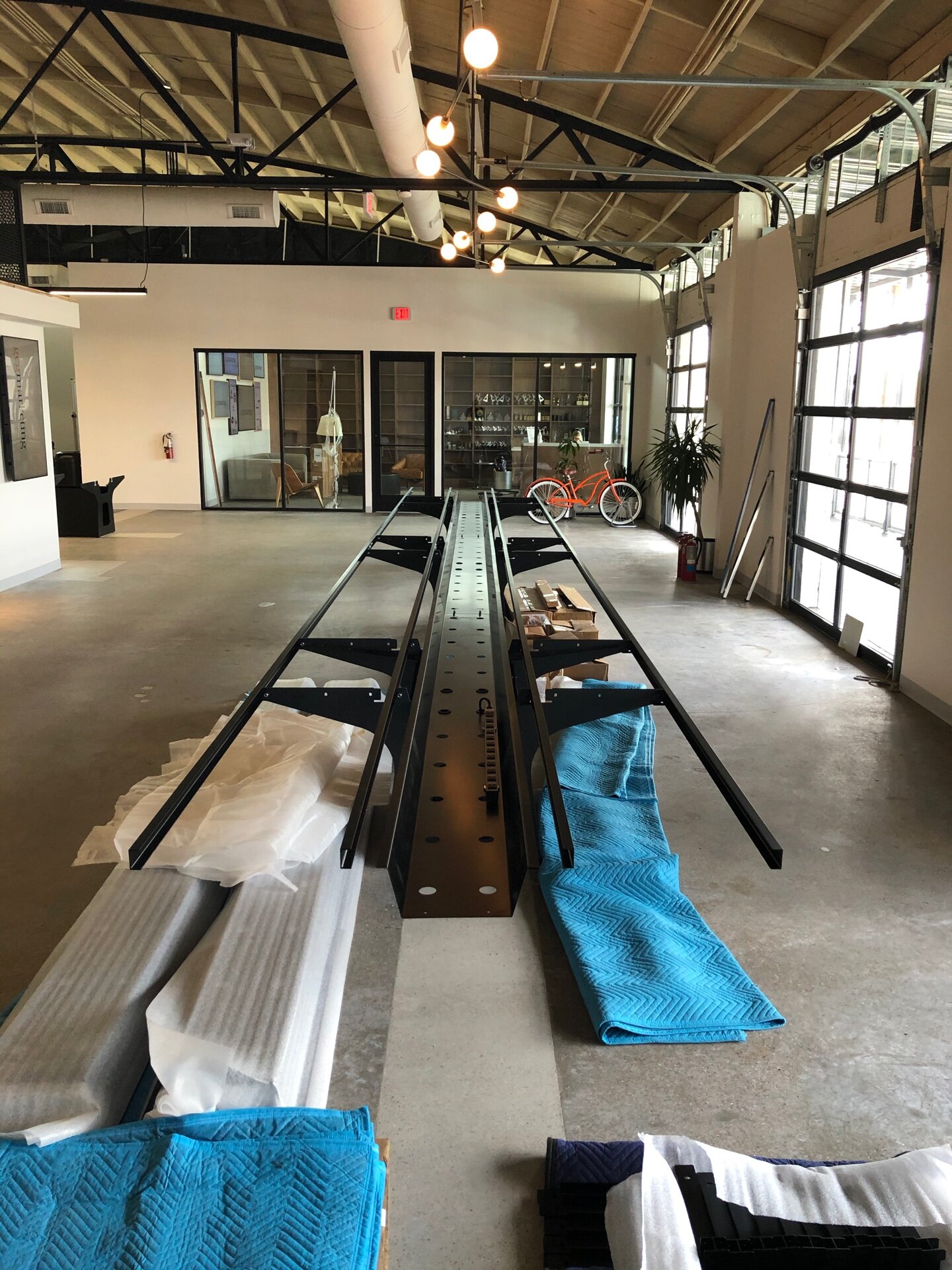
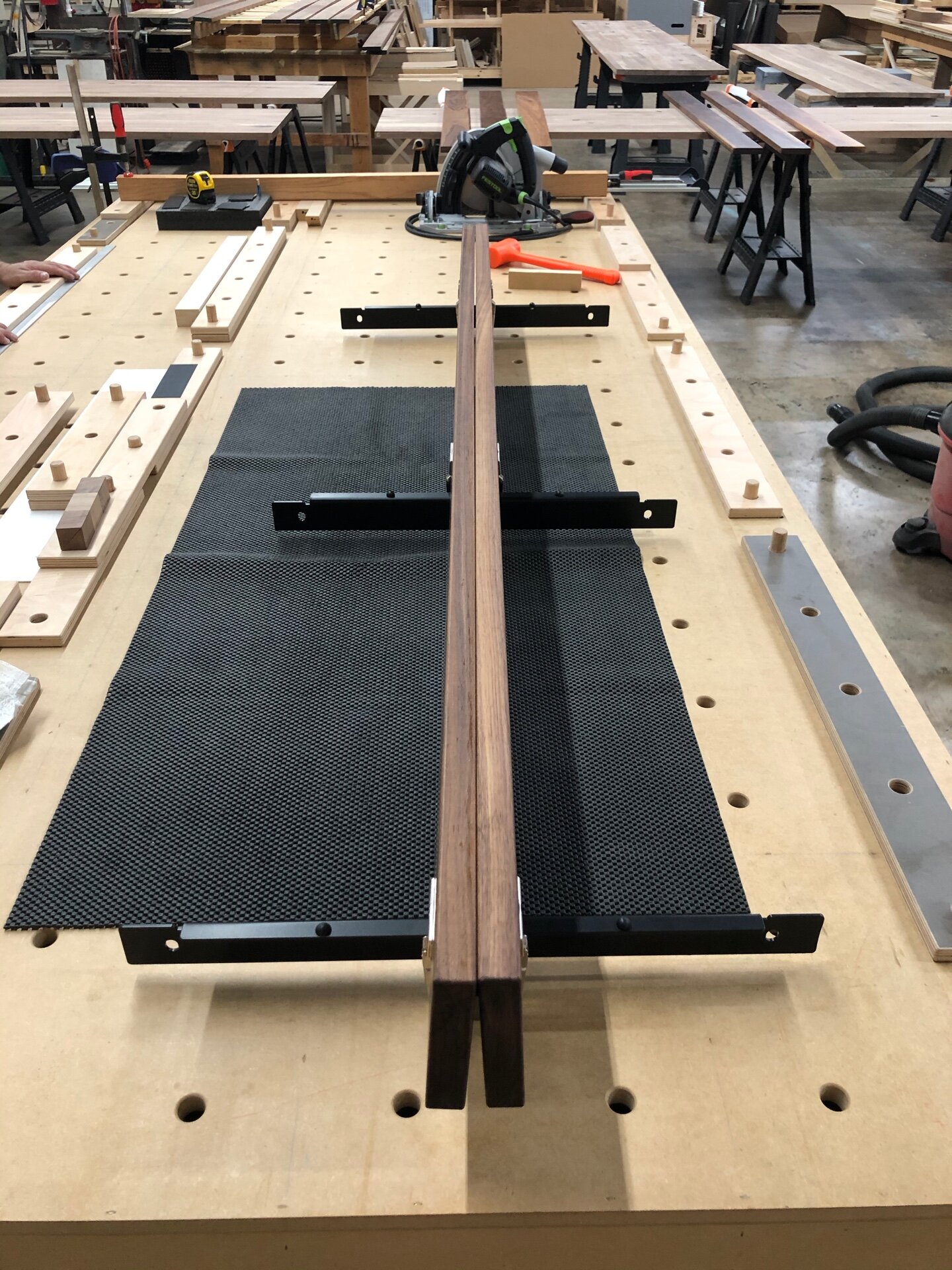
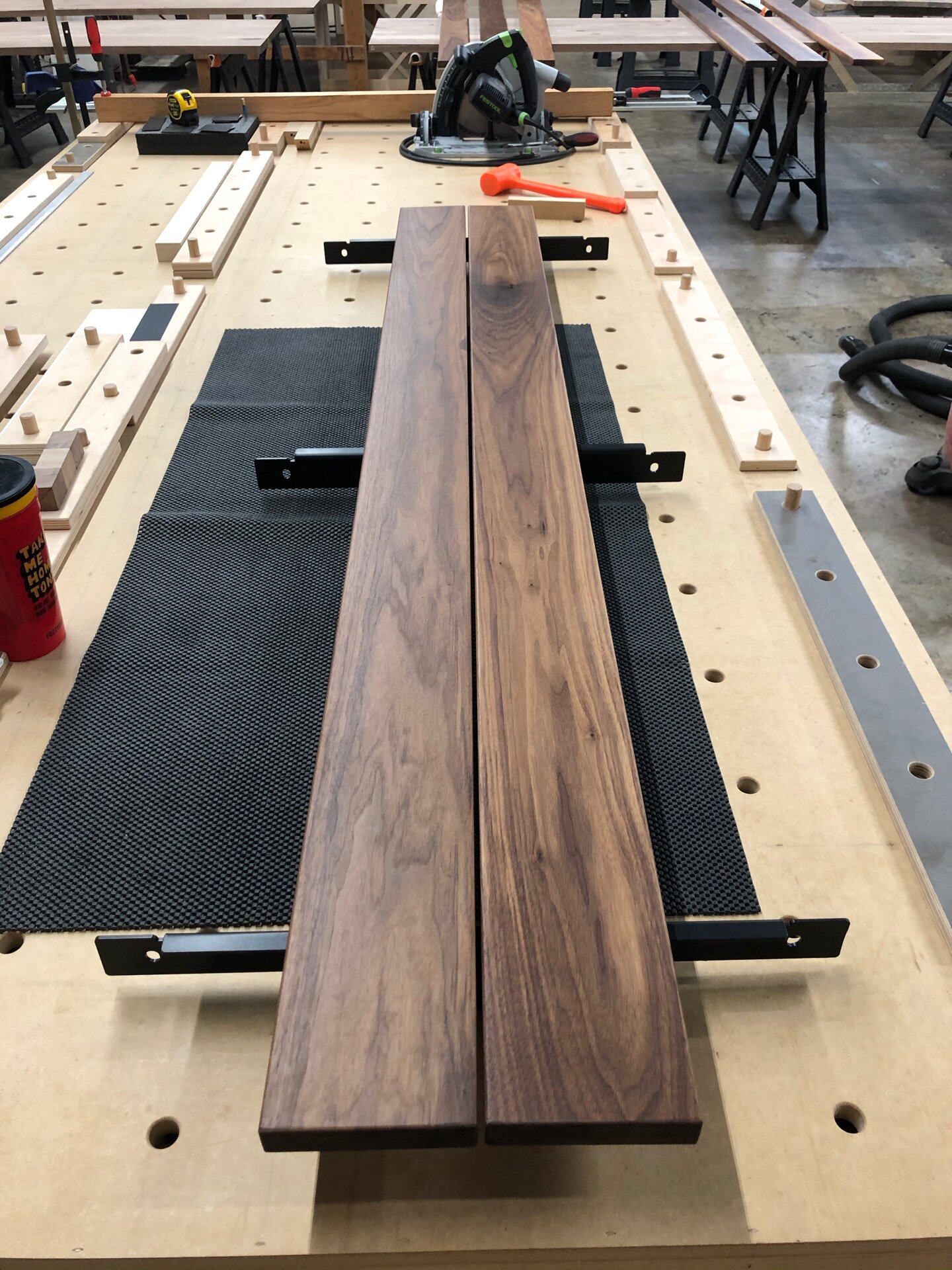
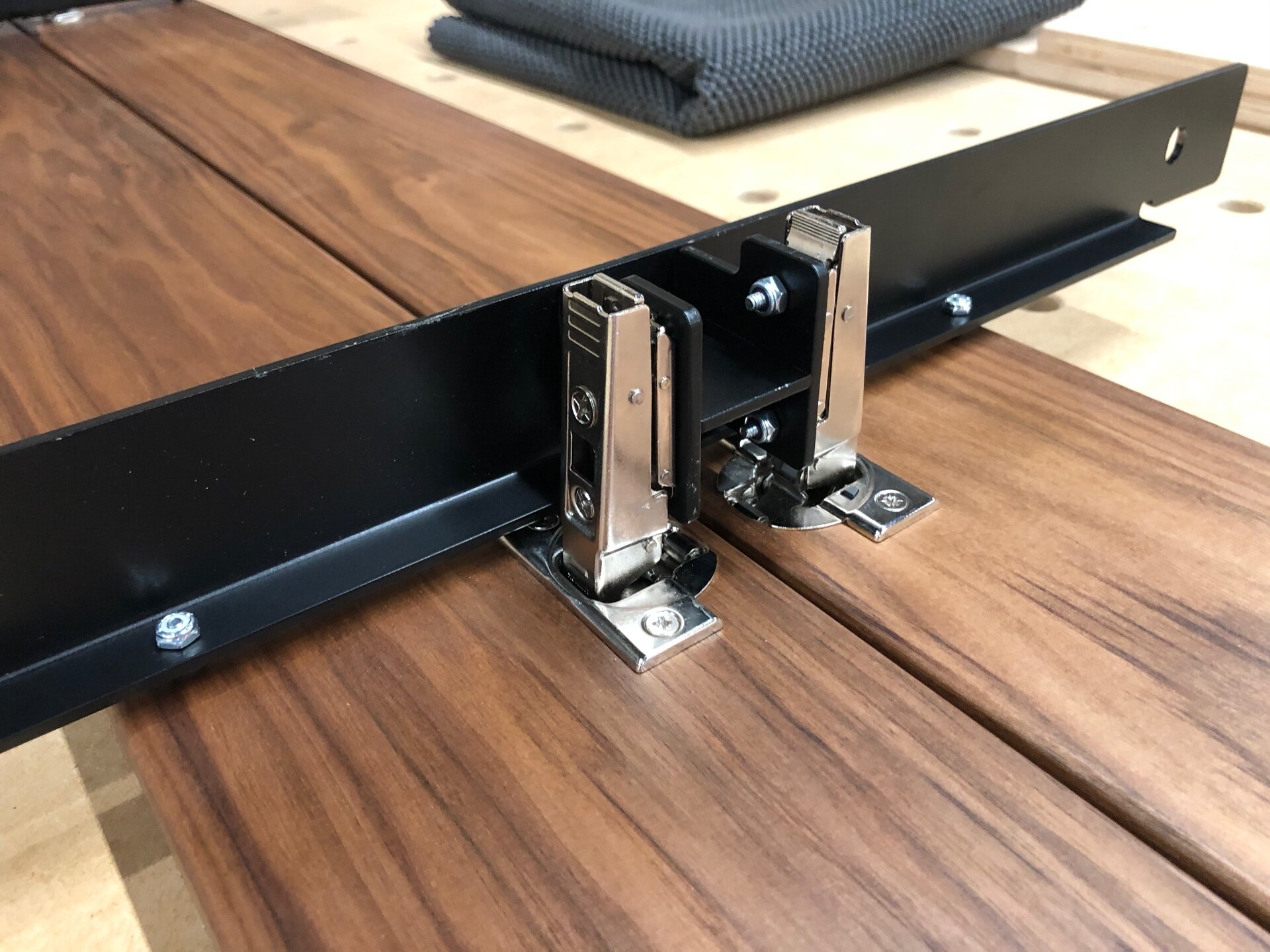